Hey R3V!
The safety nazi's at my work want to come up with a safer way to "ice-lug" machinery.
Basically Ice Lugging is when welders weld small rectangular pieces of metal onto the tracks on heavy equipment (sort of like a cleat on a soccer/football shoe) to give it more traction on snow and ice.
The current S.O.P (safe operating procedure) for Ice Lugging is in a nut shell:
-Jack up equipment, and place on stands so that tracks clear the ground
-Operator in cab rotates track on welders signal until there are lugs all the way around the track
The want to eliminate:
-The need for an operator in the cab
-The need for the welders to signal someone else to move the track, they want the moving of the track to be left to the welders so they have control over it.
Important info:
-These machines can weigh up to 150,000 lbs
-The track will rotate freely on the track frame when the engine is off, and the park brake disengaged but it takes considerable force, the tracks themselves weigh about 10,000 lbs.
-Currently it takes about 2 hours to fully ice lug a machine, if we can reduce that time then that's icing on the cake...but primarily they get massive boners for SAFETY, so we need to make this as safe as possible.
Here is a picture of a D9, probably one of the more common pieces of equipment to get ice lugged, however this also has to work for excavators, pipe-layers, etc. It needs to be a universal solution.
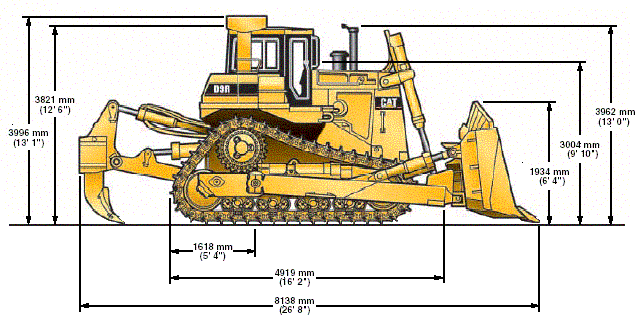
Here is a picture of Ice Lugs:

My ideas so far:
-Use an overhead crane to rotate the track. Using a 2-leg chain with grab hooks on the end you could grab the track at the bottom on the rear end and lift up, rotating the track
-Some sort of a winch system that would place a cable all the way around the track, encompassing it...and then as you reeled the winch in it would turn the track
-Some sort of a hydraulic finger built up on a telescopic stand (to account for differing machine track heights) that could insert itself in between the track ridges and spin 360 degrees, therefore rotating the track.
Anyone have any ideas?
The safety nazi's at my work want to come up with a safer way to "ice-lug" machinery.
Basically Ice Lugging is when welders weld small rectangular pieces of metal onto the tracks on heavy equipment (sort of like a cleat on a soccer/football shoe) to give it more traction on snow and ice.
The current S.O.P (safe operating procedure) for Ice Lugging is in a nut shell:
-Jack up equipment, and place on stands so that tracks clear the ground
-Operator in cab rotates track on welders signal until there are lugs all the way around the track
The want to eliminate:
-The need for an operator in the cab
-The need for the welders to signal someone else to move the track, they want the moving of the track to be left to the welders so they have control over it.
Important info:
-These machines can weigh up to 150,000 lbs
-The track will rotate freely on the track frame when the engine is off, and the park brake disengaged but it takes considerable force, the tracks themselves weigh about 10,000 lbs.
-Currently it takes about 2 hours to fully ice lug a machine, if we can reduce that time then that's icing on the cake...but primarily they get massive boners for SAFETY, so we need to make this as safe as possible.
Here is a picture of a D9, probably one of the more common pieces of equipment to get ice lugged, however this also has to work for excavators, pipe-layers, etc. It needs to be a universal solution.
Here is a picture of Ice Lugs:

My ideas so far:
-Use an overhead crane to rotate the track. Using a 2-leg chain with grab hooks on the end you could grab the track at the bottom on the rear end and lift up, rotating the track
-Some sort of a winch system that would place a cable all the way around the track, encompassing it...and then as you reeled the winch in it would turn the track
-Some sort of a hydraulic finger built up on a telescopic stand (to account for differing machine track heights) that could insert itself in between the track ridges and spin 360 degrees, therefore rotating the track.
Anyone have any ideas?
Comment