Hi.
So first time really wiring anything serious here and
out of nowhere I tested the resistance of this ring terminal I crimped
and the end of maybe 30ft of 16g.
2.3. So I soldered the terminal. Let the wire just soak up
the solder like a sponge and it came down to 0.6.
Big difference? I have no clue, but it's something.
Yeah I'm doing this on every terminal now.
Just a good idea for noobs like me that used to just crimp with cheap chinese tools and use pep-boys terminals.
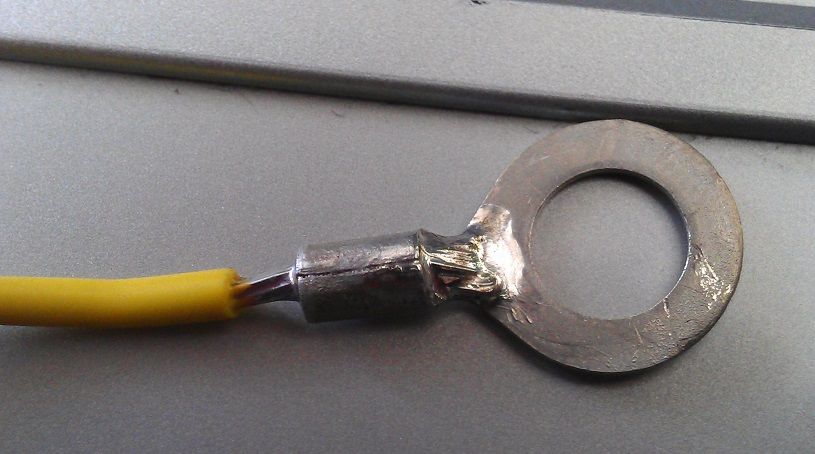
So first time really wiring anything serious here and
out of nowhere I tested the resistance of this ring terminal I crimped
and the end of maybe 30ft of 16g.
2.3. So I soldered the terminal. Let the wire just soak up
the solder like a sponge and it came down to 0.6.
Big difference? I have no clue, but it's something.
Yeah I'm doing this on every terminal now.
Just a good idea for noobs like me that used to just crimp with cheap chinese tools and use pep-boys terminals.
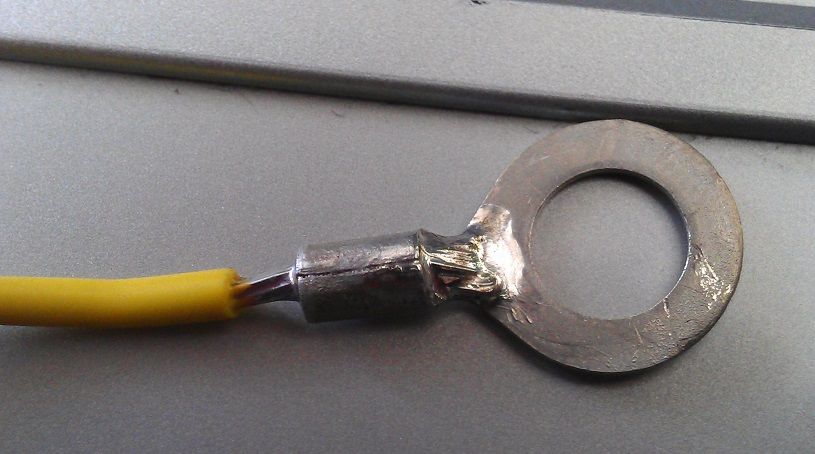
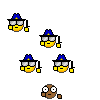
Comment