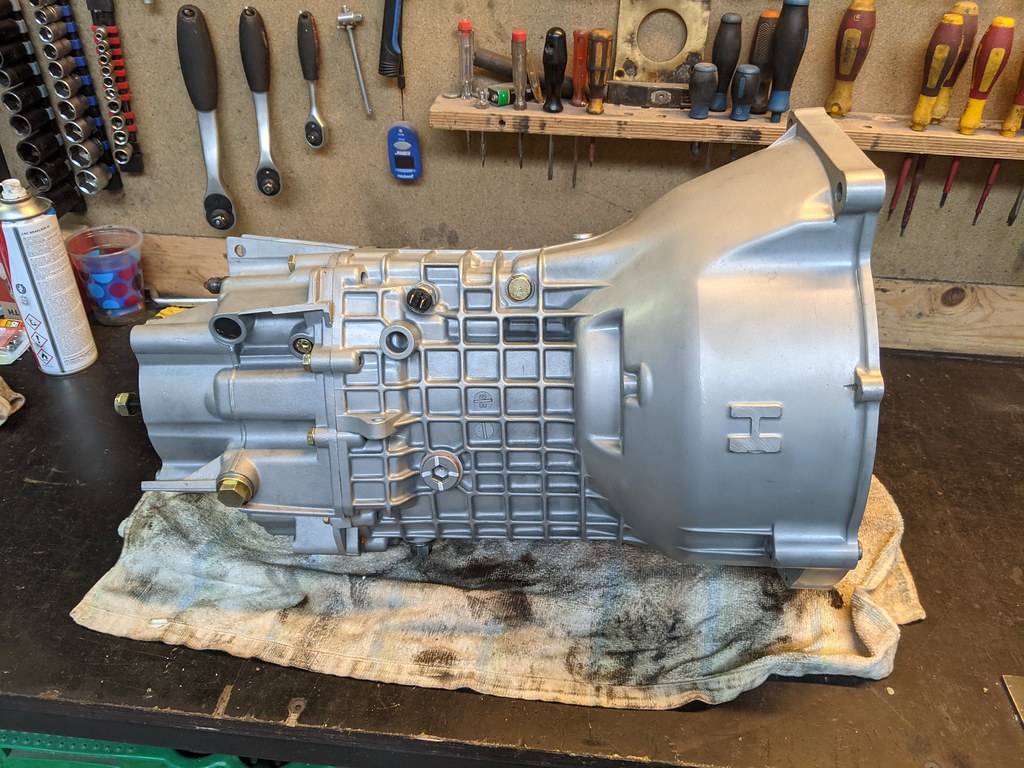


I already mounted the pivot arm and throw out bearing + shifter
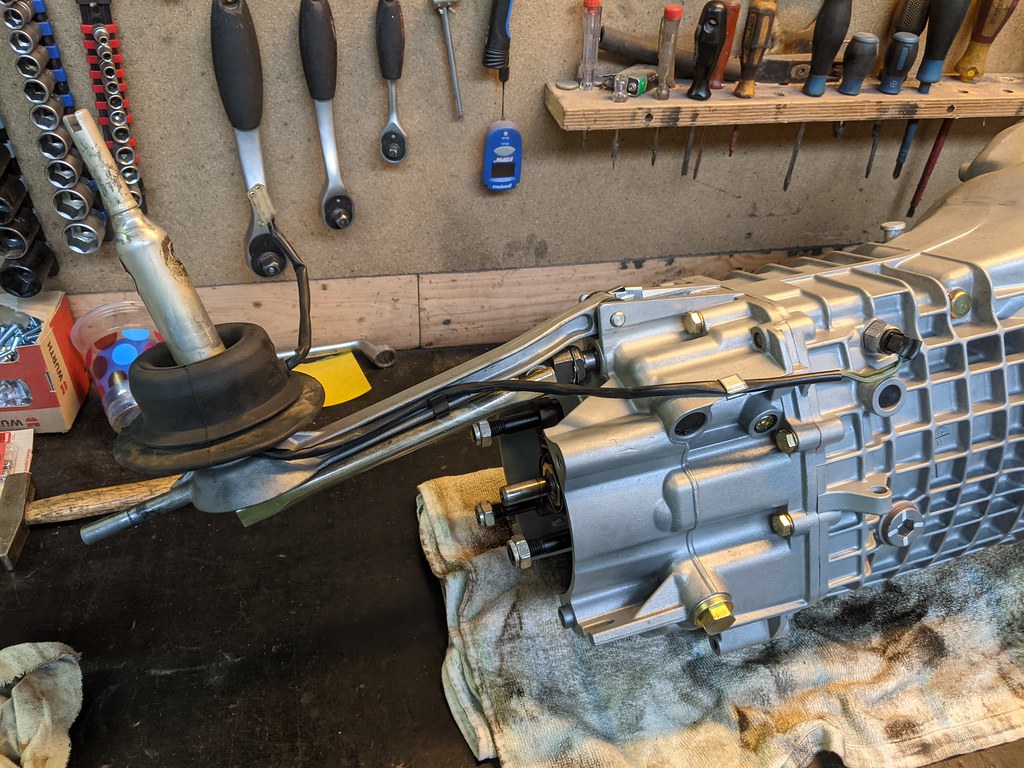
I was able to get some old E36 tie rods from a friend to test/modify them in order to get the same overall length from tie rod end to tie rod end. stock iX is +/- 1380m
E36 tie rod is already a bit shorter but in order to get to the stock overall length, I had to remove 20mm from the X3 inner tie rods. I might remove a little more as they are now fully bottomed out on the threads - so I have some more room to get the toe right.

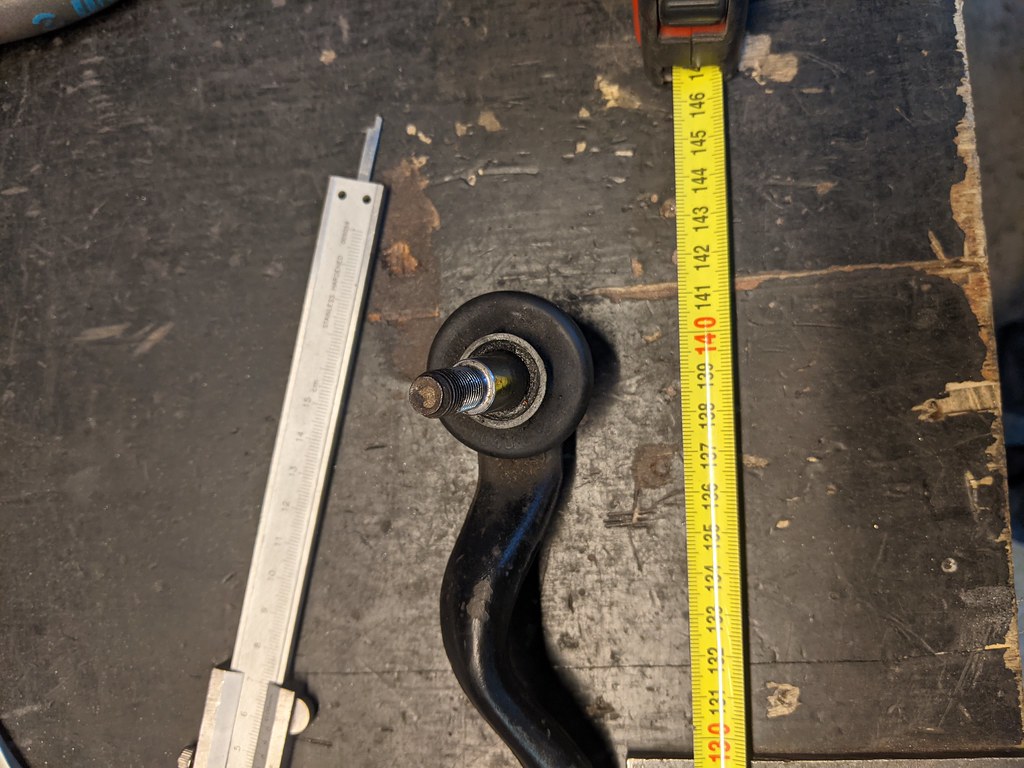
Leave a comment: