A big box of goodies from Tischer / BMW of Silver Spring showed up today, so I have almost everything that I need to put it all back together. Before I can do that though, I need to take the flywheel and pressure plate to the machine shop for dynamic balancing, so I assume that next week will be when I start turning wrenches in earnest. I think that I will mostly leave the accessories and stuff not bolted on to the engine just to make it a little easier to shoe-horn back in to the car, and the same goes for the engine wiring harness. Having that and the firewall cable tray out actually gives me that last bit of clearance that should make the reinstall a breeze (it often hangs up on the cable tray & wiring umbilical when those are present).
Thankfully, the M42 engine mounts that I got were manufactured correctly, so there is no need for poly ones. Maybe BMW Canada has different suppliers or it was just a bad batch or something.
Also, I put the pad wear sensor connector back together this evening. These connectors are a big pain the ass. If someone wants the step-by-step instructions I can type them out, but the short story is that these are one type of connector that you sort of want the specialty tool for. I managed without it, but it involved unconventional assembly. The terminals are an interference fit inside the rubber housing, and you have to push them really really hard to get them buried all the way up where they belong. I fed the wires through, crimped the terminals on and then forced them in from the front since the forward part of these things is a hell of a lot more sturdy than the part that the wire is crimped onto, and I used isopropyl alcohol as the lubricant per the manufacturer's recommendation. Naturally I forced one too far, and I ended up brute forcing it into place with some very small needle nosed pliers from the back side.
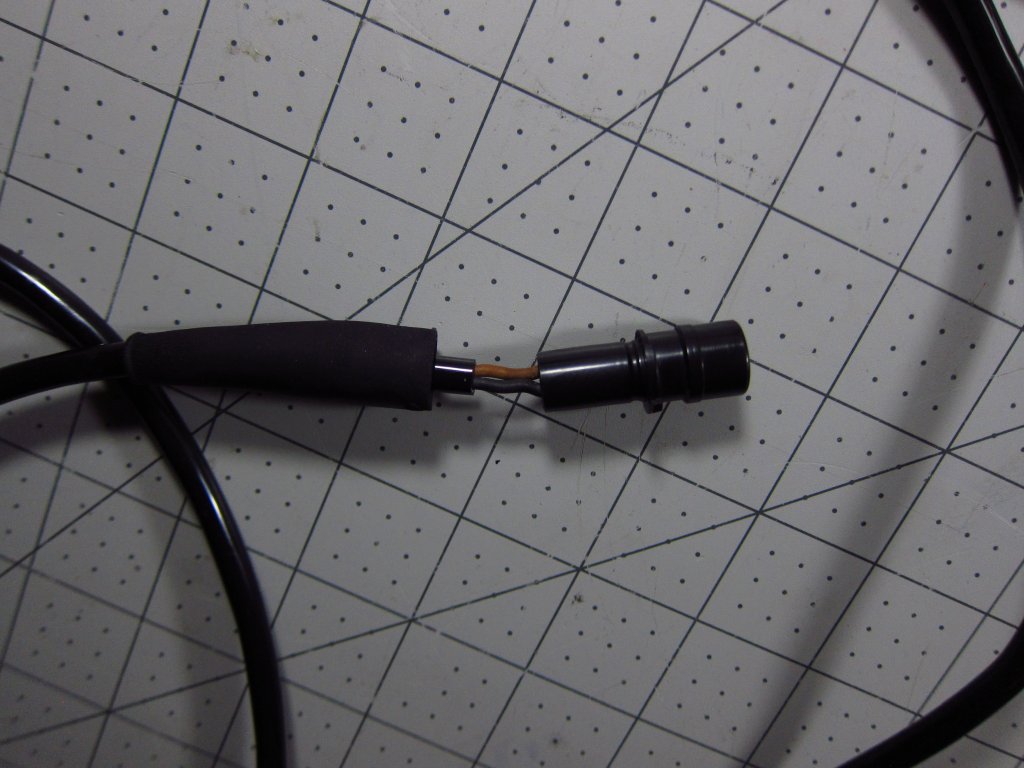
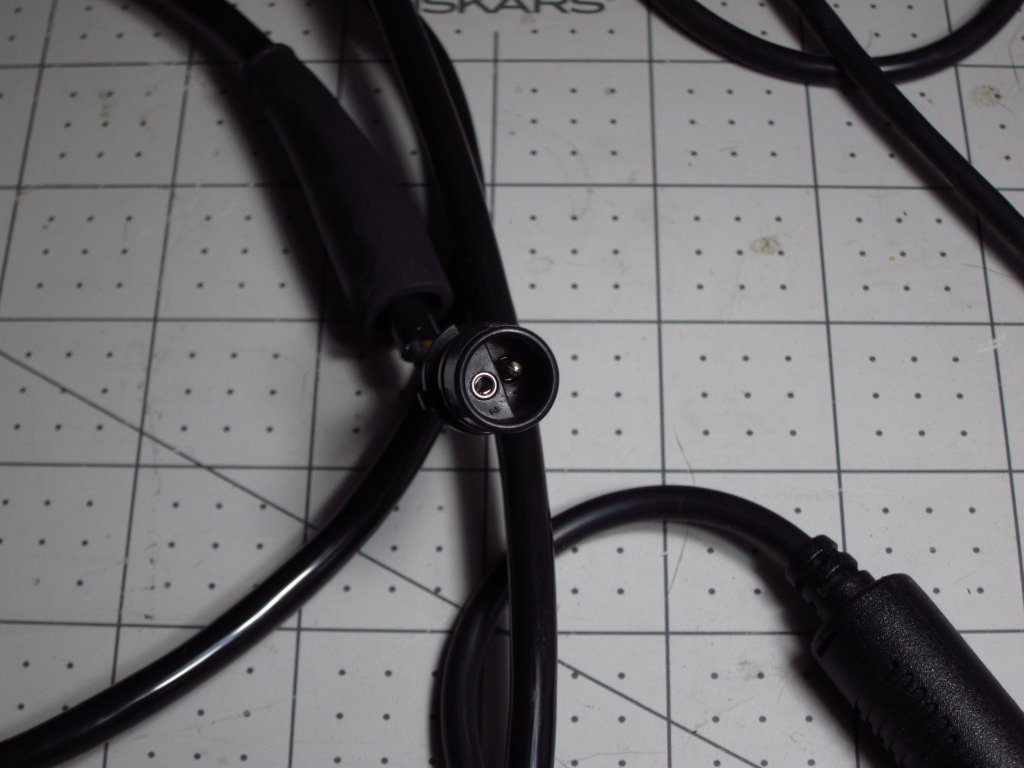
In other news, I ripped out all the power wiring for my sound system and redesigned how I want it all to route. Everything worked fine before, but there was a jumble of fuse holders and wiring next to the battery which I disliked. I'll detail the new wire routing scheme in my car audio thread, but basically it will all run along the driver's side fender in the outermost bulkhead cavity, with a 3D printed fuse holder mounted to the gas door lock solenoid bracket. This way everything will tuck up inside behind the side panel covering, guide the cables and eliminate the mess that was by the battery (I did the sound system & wiring back in 2008/9 and was a lot less competent then).
The first version is in the printer now. The new fuse holders and power cable are coming from Parts Express, so I made models based on the existing stuff. An hour or so with calipers was all that was needed to get the lock solenoid and its bracket modeled well enough to work with. Once I get the actual stuff I will update the base models, and it should all regenerate properly since the big holder/bracket part is fully top-down parametric with the stuff around it. At ~7.5 hours per print I'd prefer not to have to tweak the design more than once or twice.
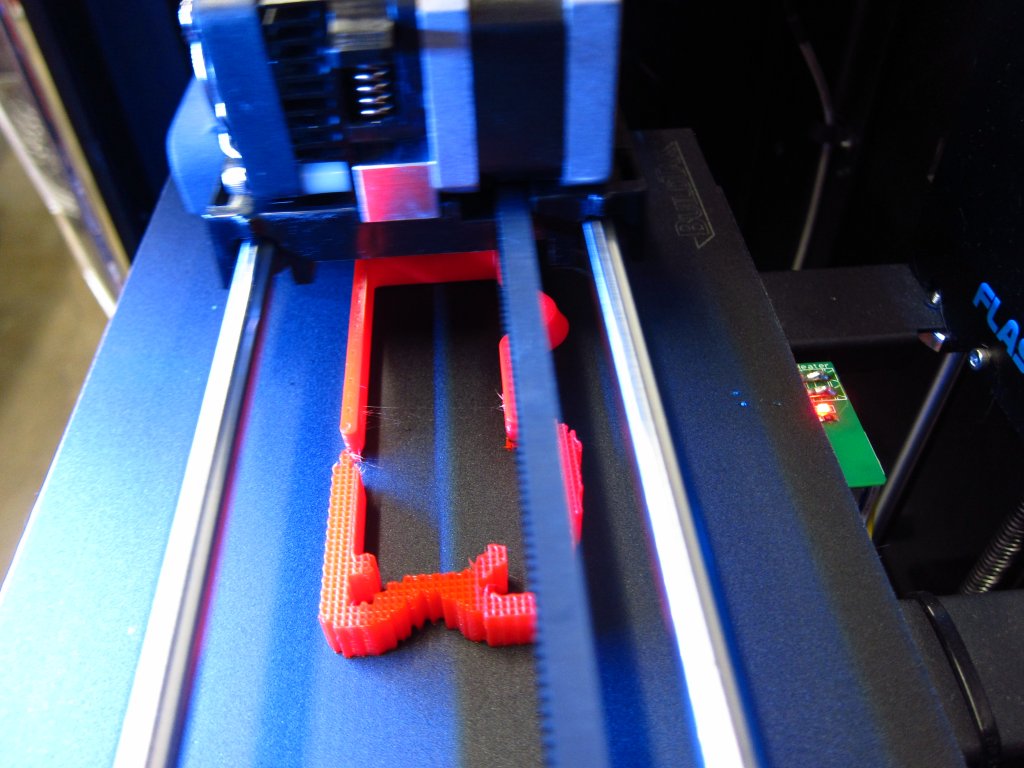
The big green fuse holder has the 60A fuse for my 5CH amplifier, and the 2 smaller teal ones have 5A fuses for my 3-way active crossover and the RMT-200 head unit (I am running dedicated power & ground to it all the way from the battery since the factory power & ground are not entirely optimal). The red bracket ended up looking like a space ship from the original Homeworld games IMO.
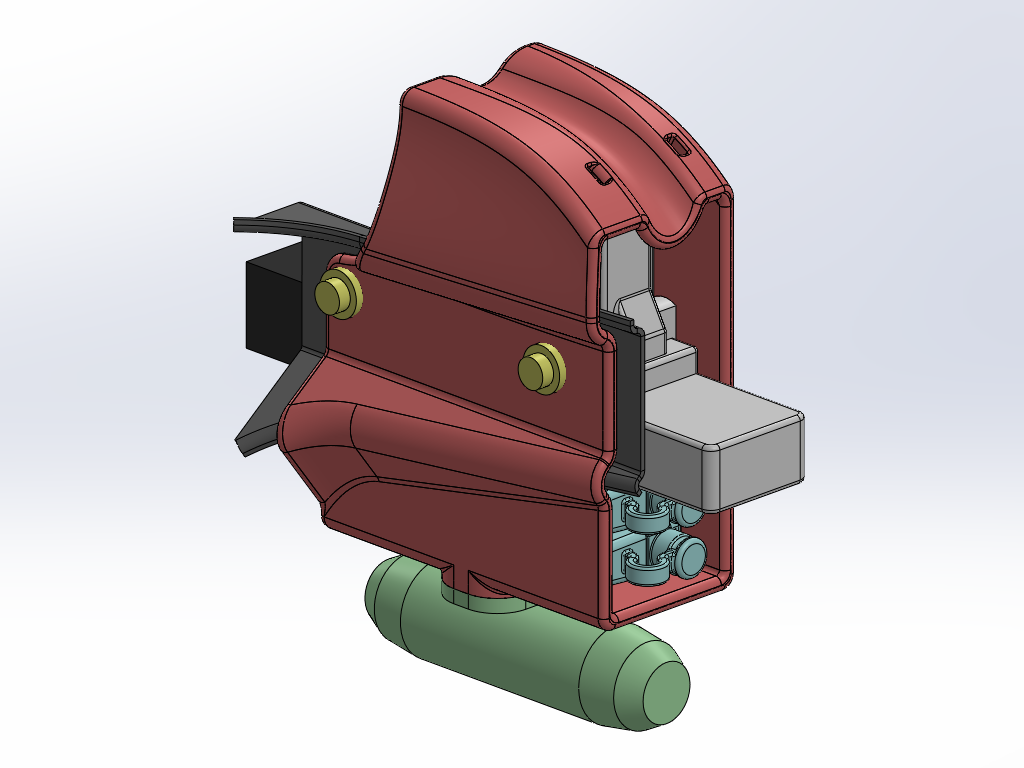
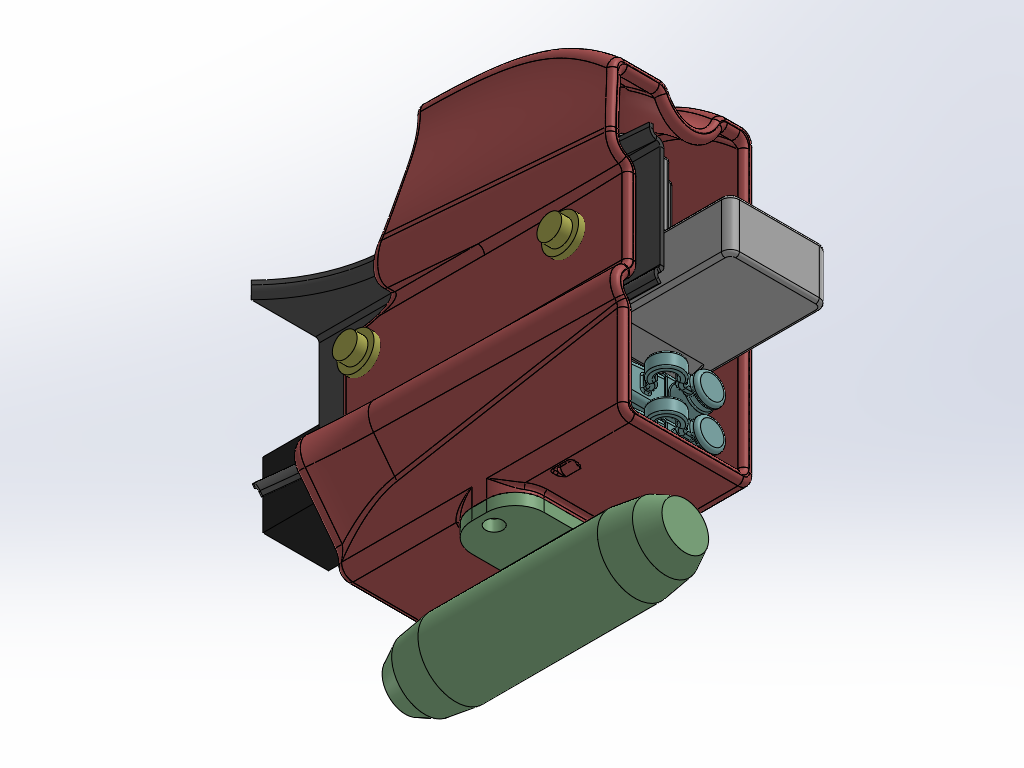
I spent a bit of time in Simplify3D getting the slicing optimized for the part. My printer is a Flashforge Creator Pro that I have modified fairly extensively (removed second extruder to eliminate vibration, installed TMC2209 stepper drivers for smooth silent operation using custom designed PCBs, designed a clip-on dial indicator holder for precision leveling, used brass shims to remove guide rail slop at ends). It is a decent printer out of the box, but it is a lot better now with the changes and a couple of days spent optimizing the print settings with some test pieces.
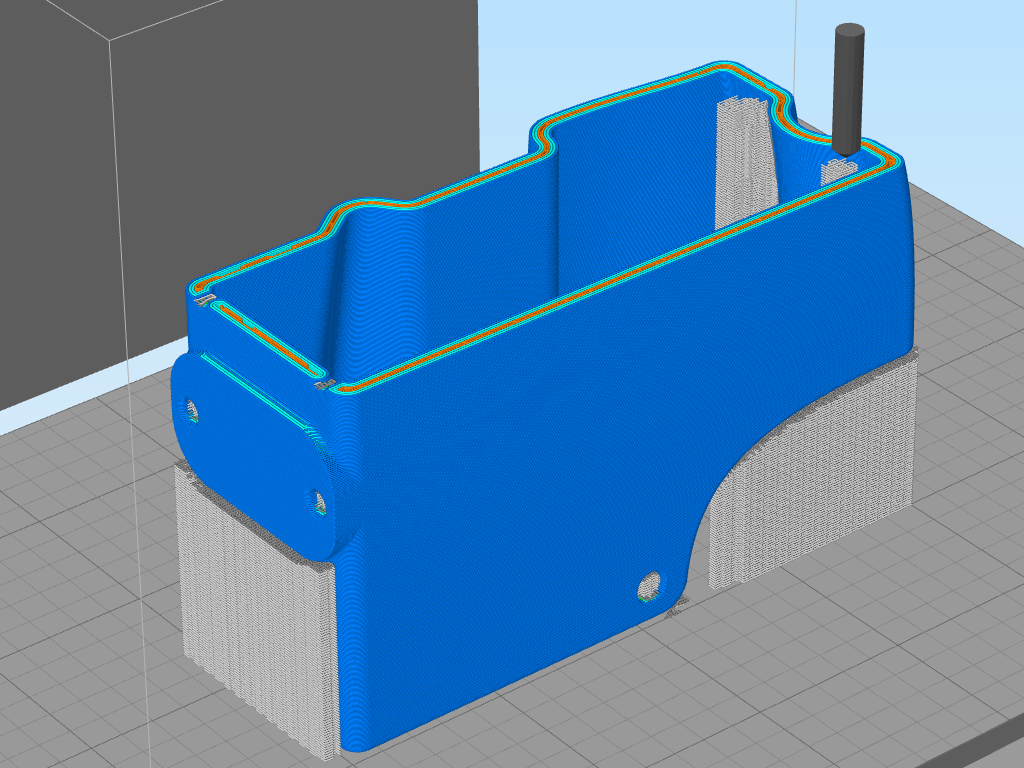
Anyway, I will continue updating as I make progress, whether it be with the actual original topic of the thread (getting the stupid thing running) or other too-much-time-on-my-hands nonsense.
Thankfully, the M42 engine mounts that I got were manufactured correctly, so there is no need for poly ones. Maybe BMW Canada has different suppliers or it was just a bad batch or something.
Also, I put the pad wear sensor connector back together this evening. These connectors are a big pain the ass. If someone wants the step-by-step instructions I can type them out, but the short story is that these are one type of connector that you sort of want the specialty tool for. I managed without it, but it involved unconventional assembly. The terminals are an interference fit inside the rubber housing, and you have to push them really really hard to get them buried all the way up where they belong. I fed the wires through, crimped the terminals on and then forced them in from the front since the forward part of these things is a hell of a lot more sturdy than the part that the wire is crimped onto, and I used isopropyl alcohol as the lubricant per the manufacturer's recommendation. Naturally I forced one too far, and I ended up brute forcing it into place with some very small needle nosed pliers from the back side.
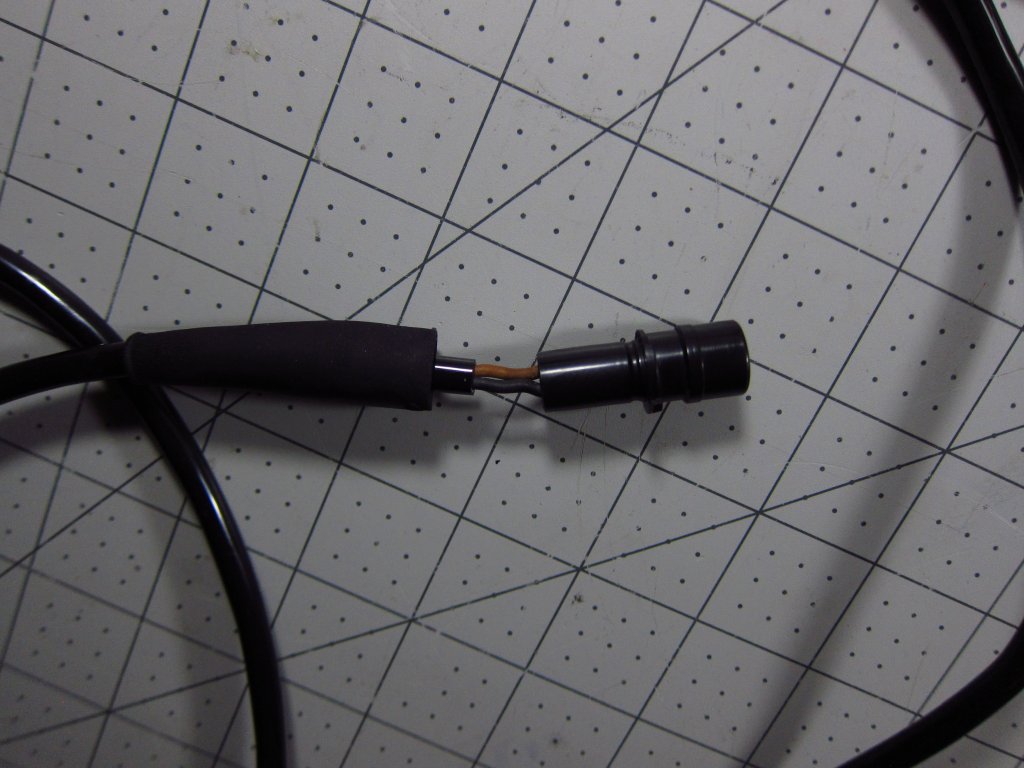
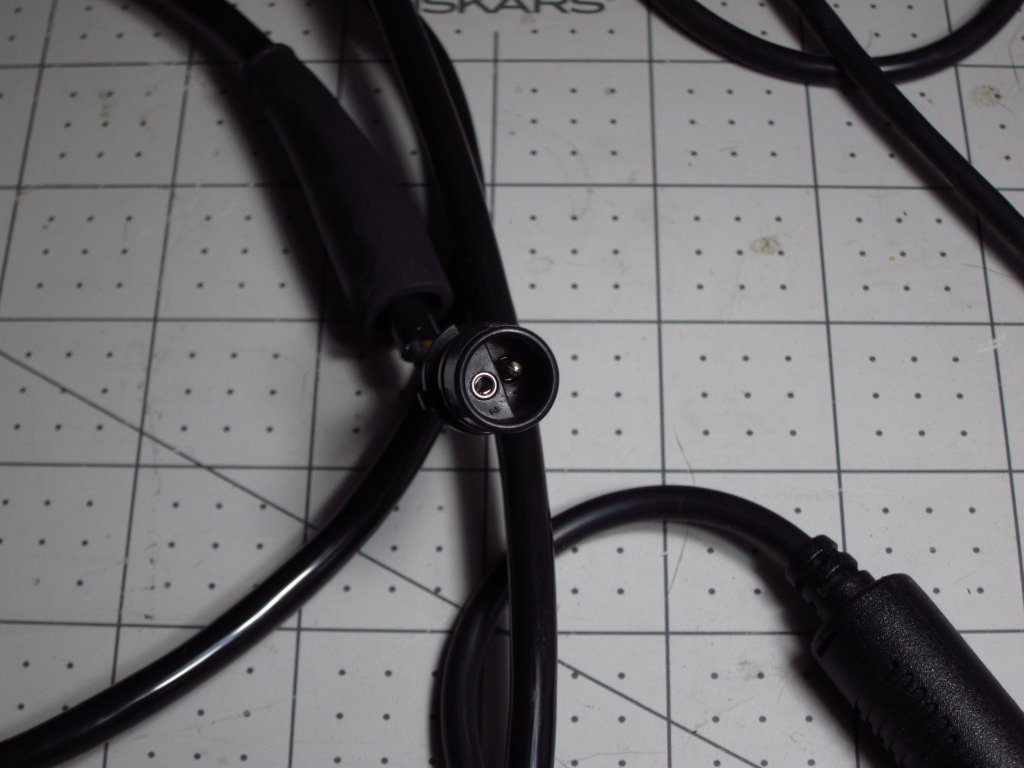
In other news, I ripped out all the power wiring for my sound system and redesigned how I want it all to route. Everything worked fine before, but there was a jumble of fuse holders and wiring next to the battery which I disliked. I'll detail the new wire routing scheme in my car audio thread, but basically it will all run along the driver's side fender in the outermost bulkhead cavity, with a 3D printed fuse holder mounted to the gas door lock solenoid bracket. This way everything will tuck up inside behind the side panel covering, guide the cables and eliminate the mess that was by the battery (I did the sound system & wiring back in 2008/9 and was a lot less competent then).
The first version is in the printer now. The new fuse holders and power cable are coming from Parts Express, so I made models based on the existing stuff. An hour or so with calipers was all that was needed to get the lock solenoid and its bracket modeled well enough to work with. Once I get the actual stuff I will update the base models, and it should all regenerate properly since the big holder/bracket part is fully top-down parametric with the stuff around it. At ~7.5 hours per print I'd prefer not to have to tweak the design more than once or twice.
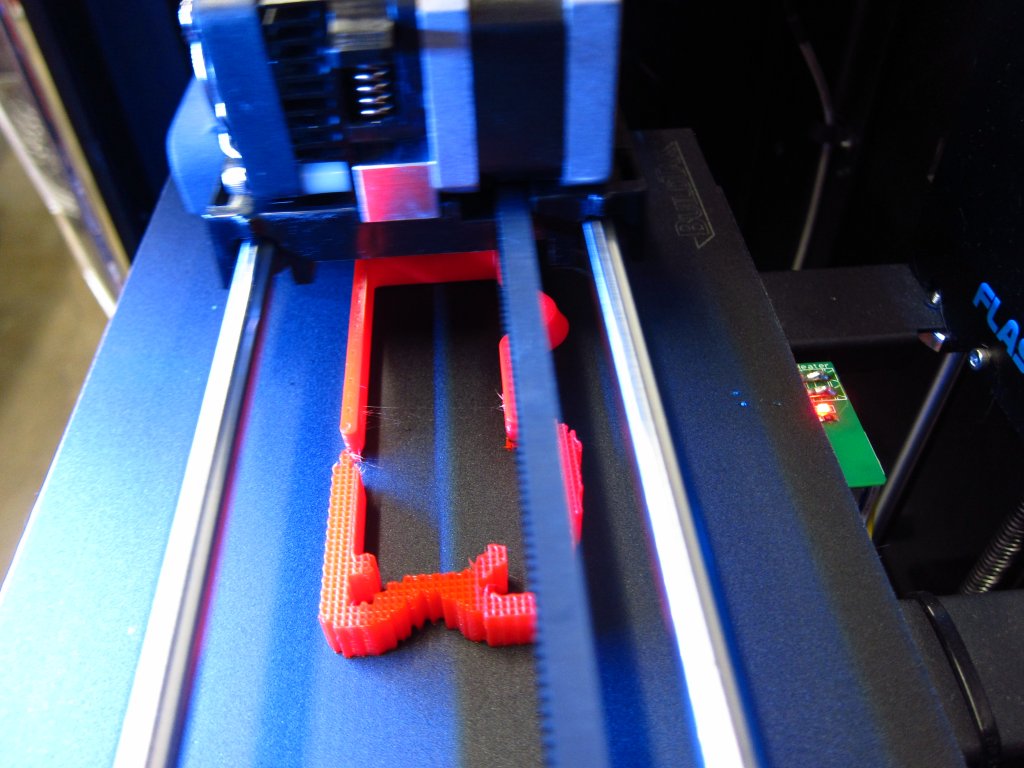
The big green fuse holder has the 60A fuse for my 5CH amplifier, and the 2 smaller teal ones have 5A fuses for my 3-way active crossover and the RMT-200 head unit (I am running dedicated power & ground to it all the way from the battery since the factory power & ground are not entirely optimal). The red bracket ended up looking like a space ship from the original Homeworld games IMO.
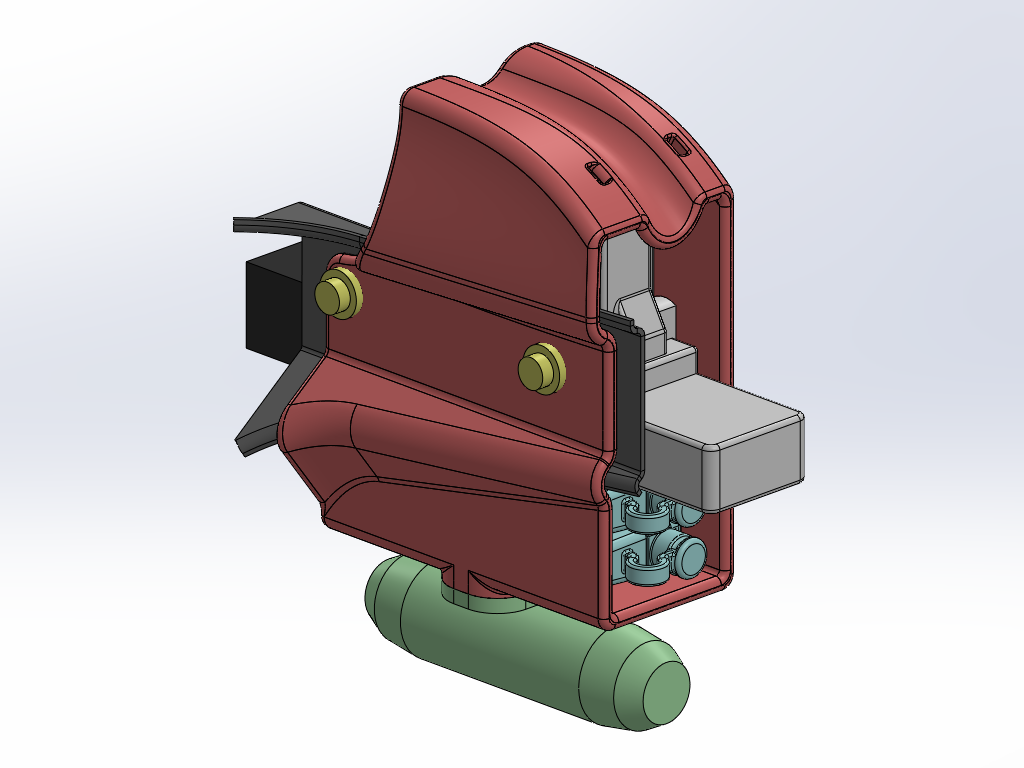
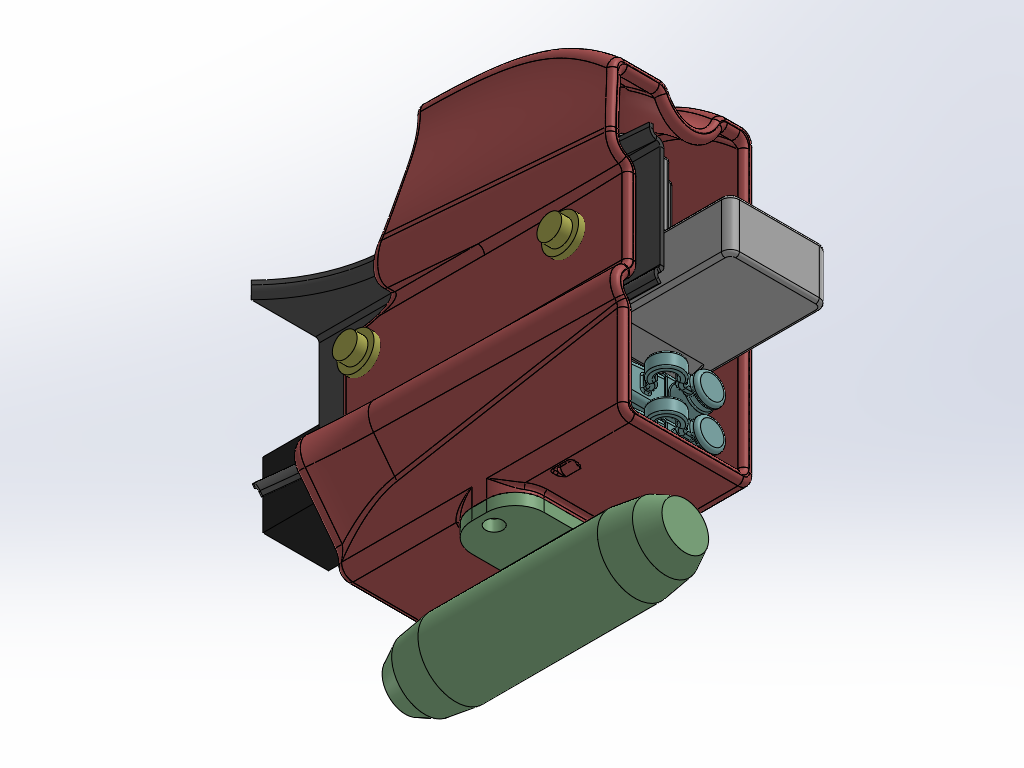
I spent a bit of time in Simplify3D getting the slicing optimized for the part. My printer is a Flashforge Creator Pro that I have modified fairly extensively (removed second extruder to eliminate vibration, installed TMC2209 stepper drivers for smooth silent operation using custom designed PCBs, designed a clip-on dial indicator holder for precision leveling, used brass shims to remove guide rail slop at ends). It is a decent printer out of the box, but it is a lot better now with the changes and a couple of days spent optimizing the print settings with some test pieces.
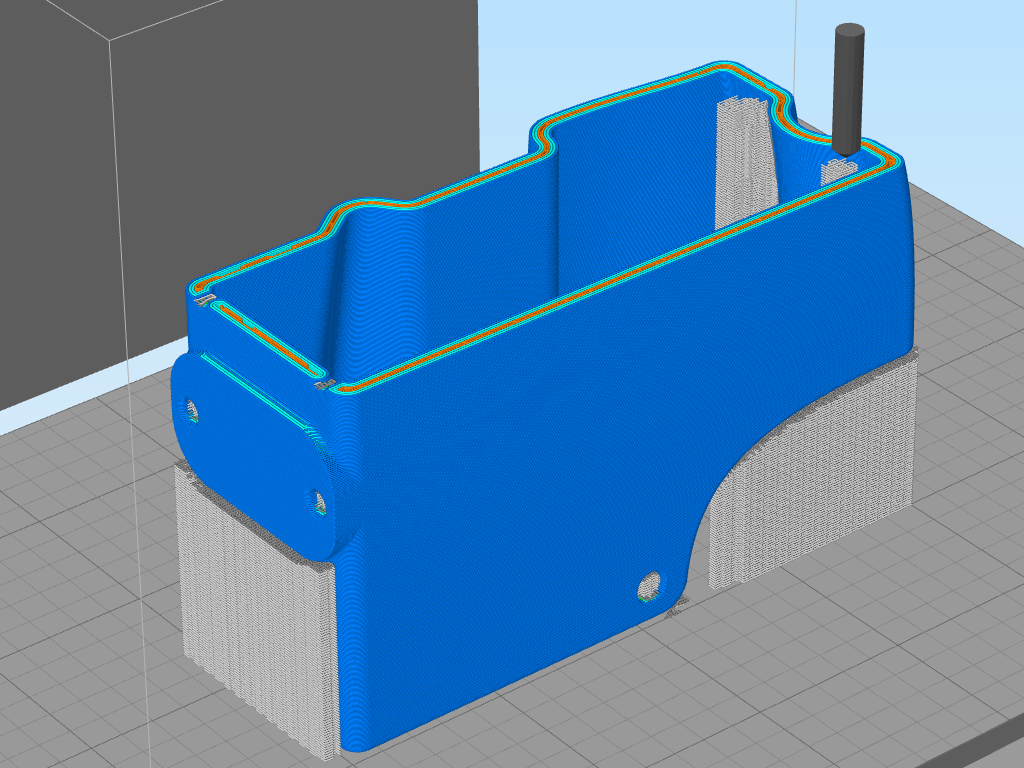
Anyway, I will continue updating as I make progress, whether it be with the actual original topic of the thread (getting the stupid thing running) or other too-much-time-on-my-hands nonsense.
Comment