Carbide cutter to the rescue. It made short work of cleaning up the hole that ate my drill bits. It was easy enough to finish this up on the drill press after a little work to make sure that the cutter was centered. The threads cut nice and smoothly.
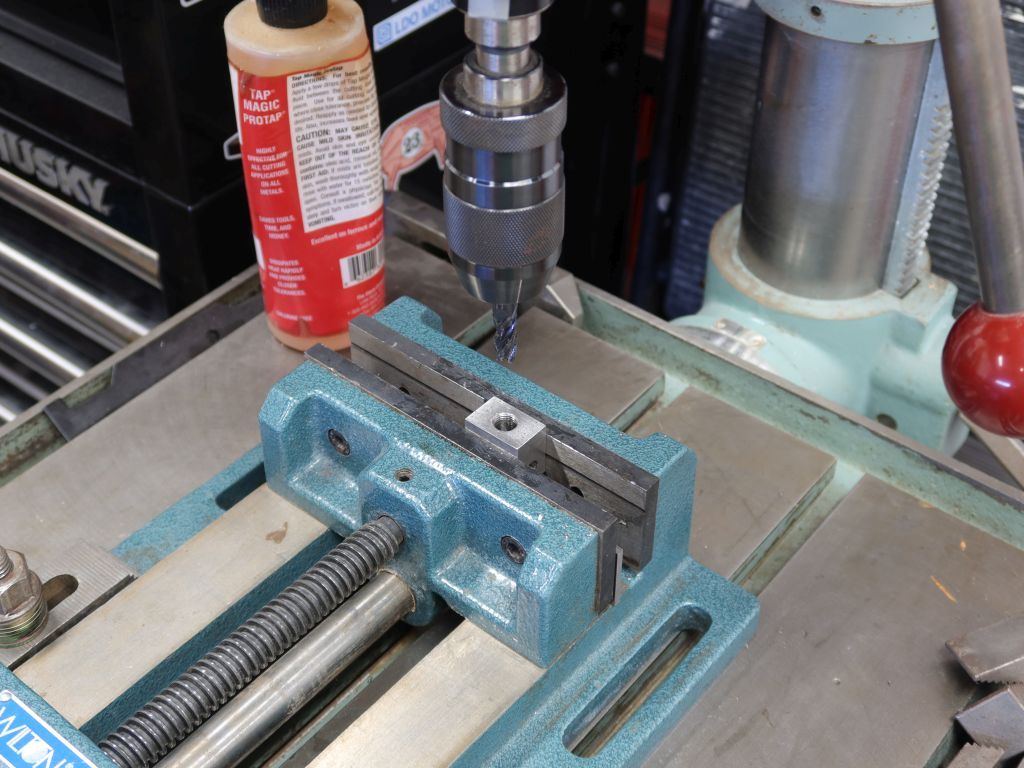
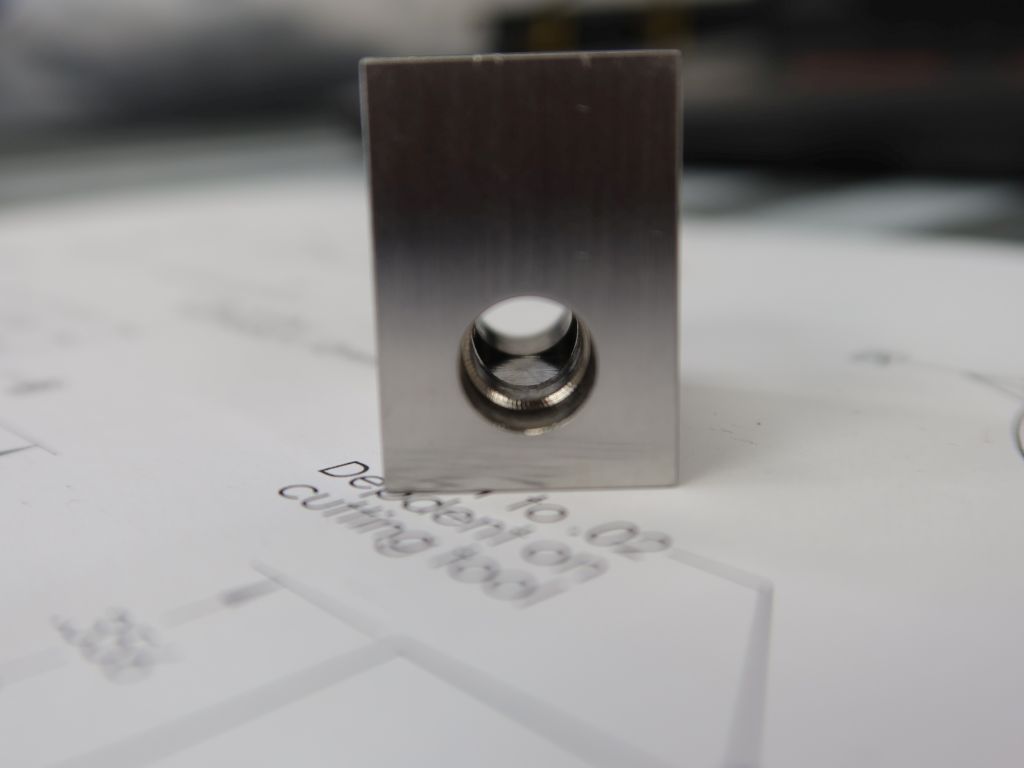
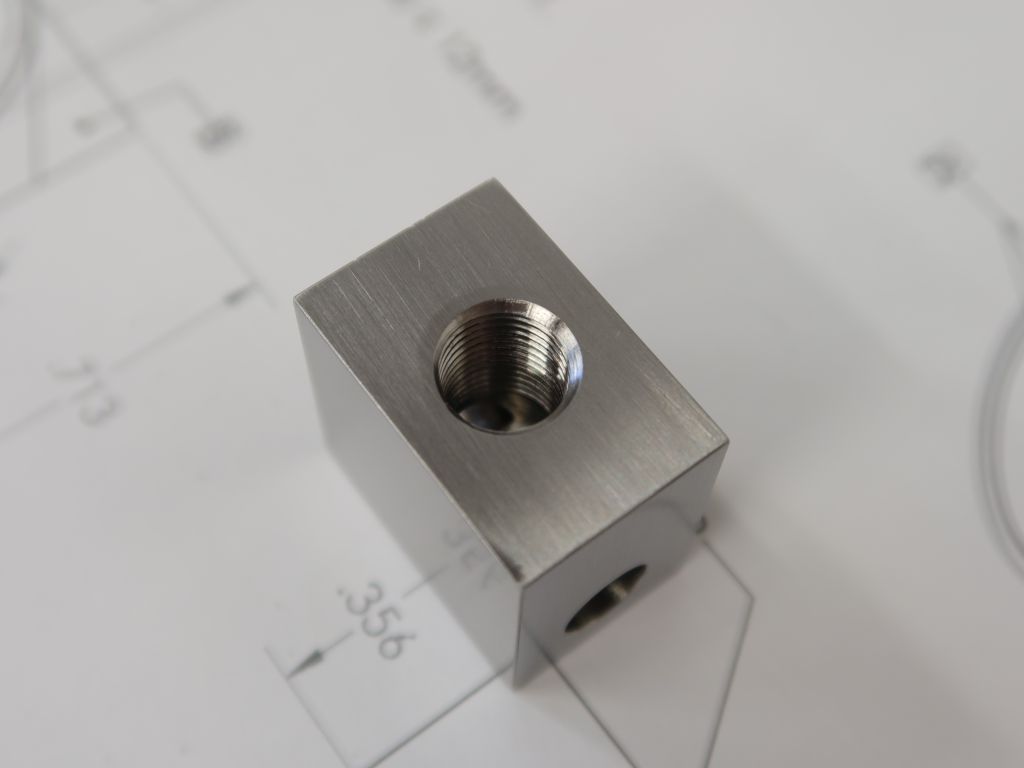
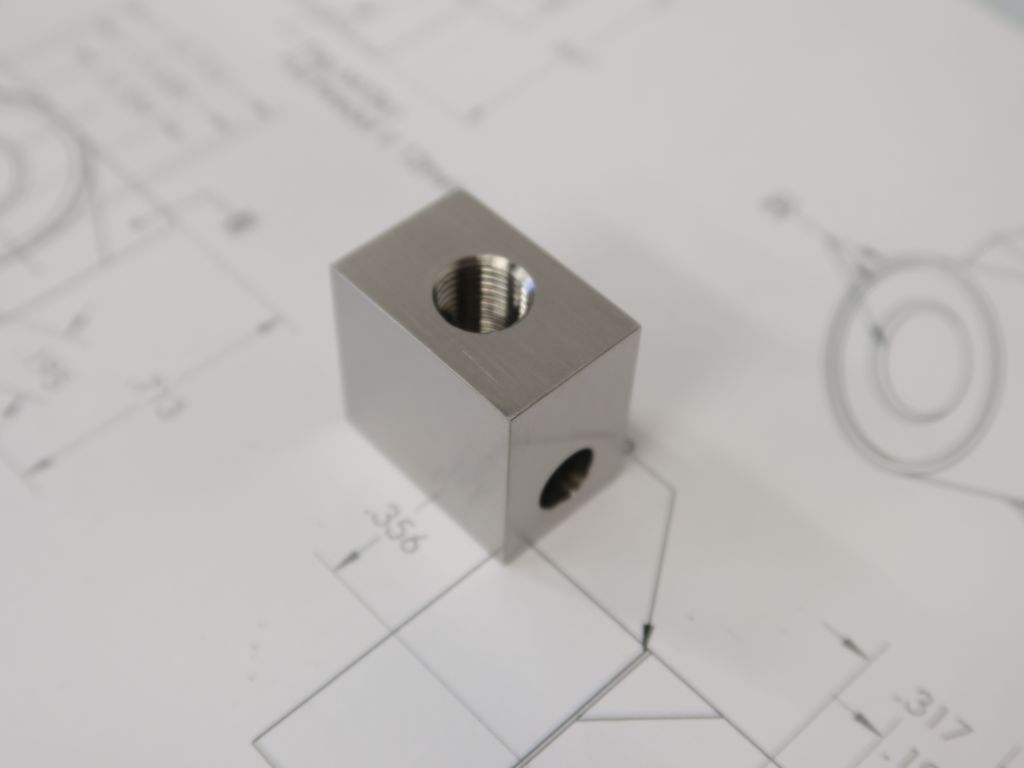
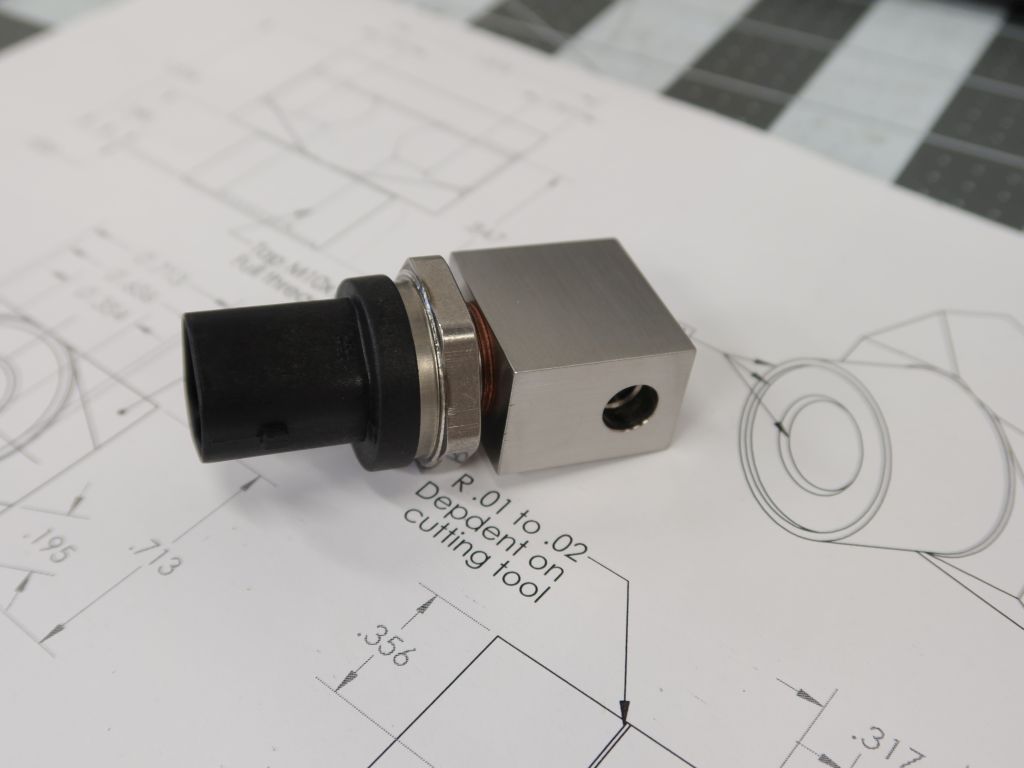
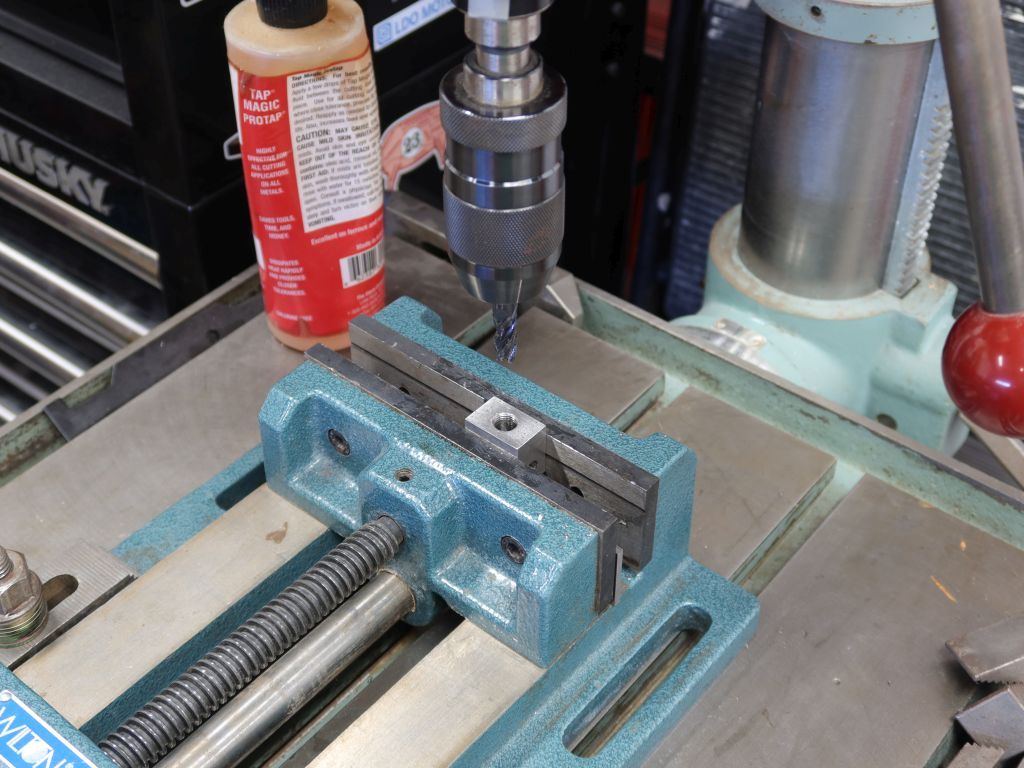
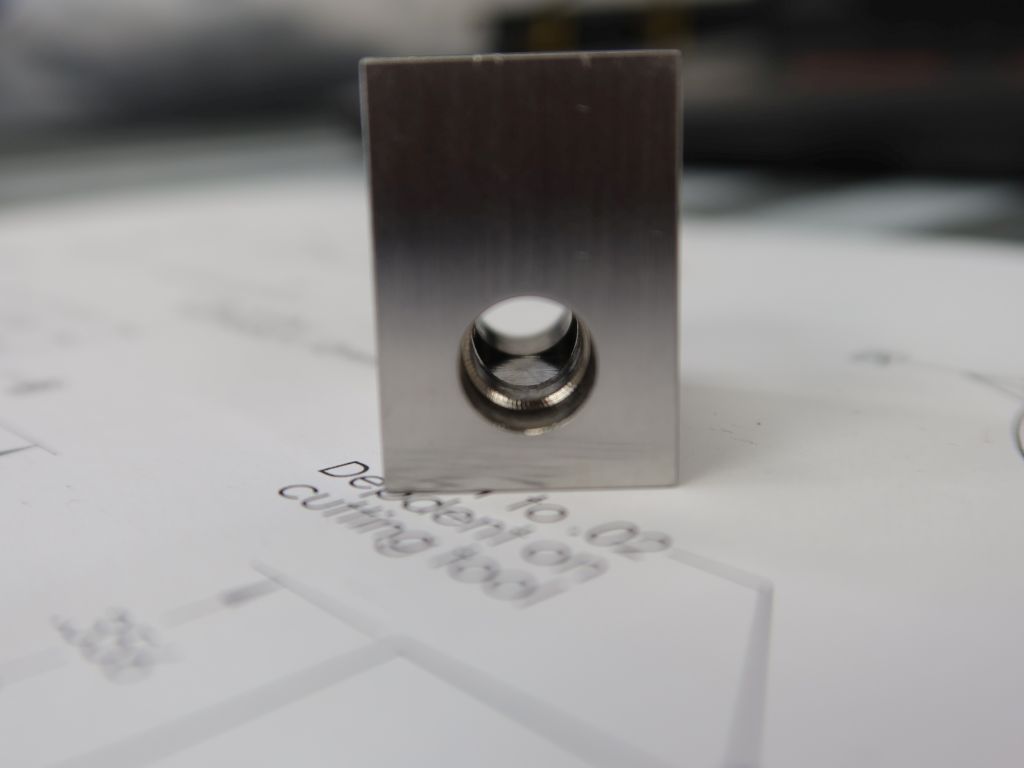
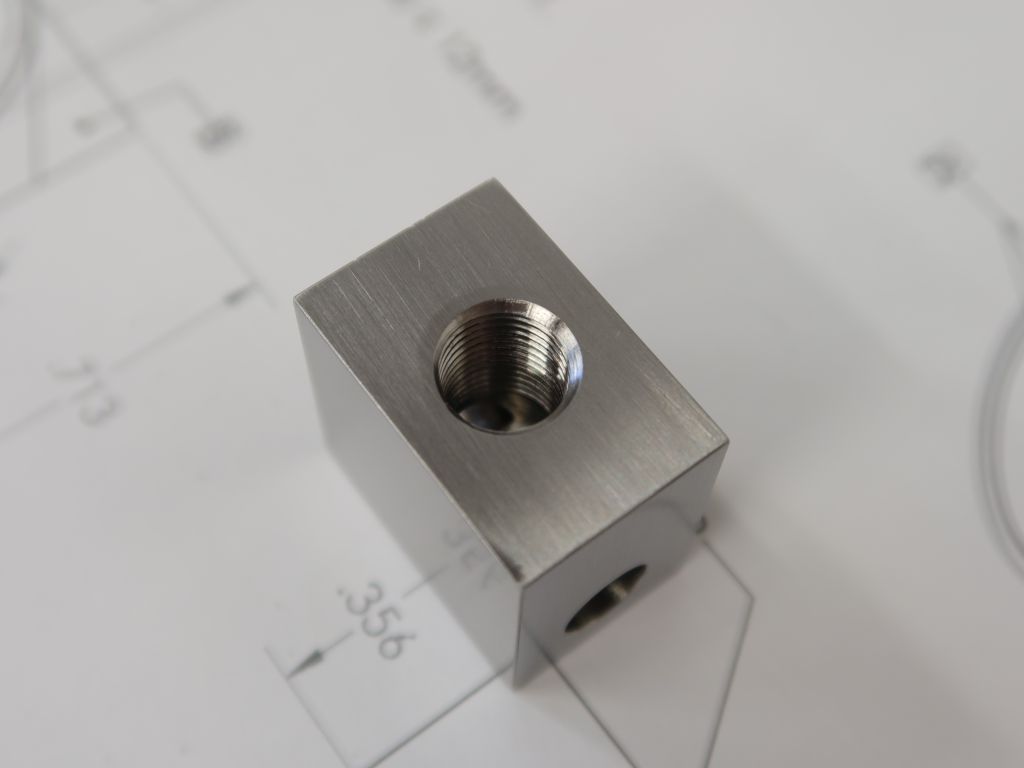
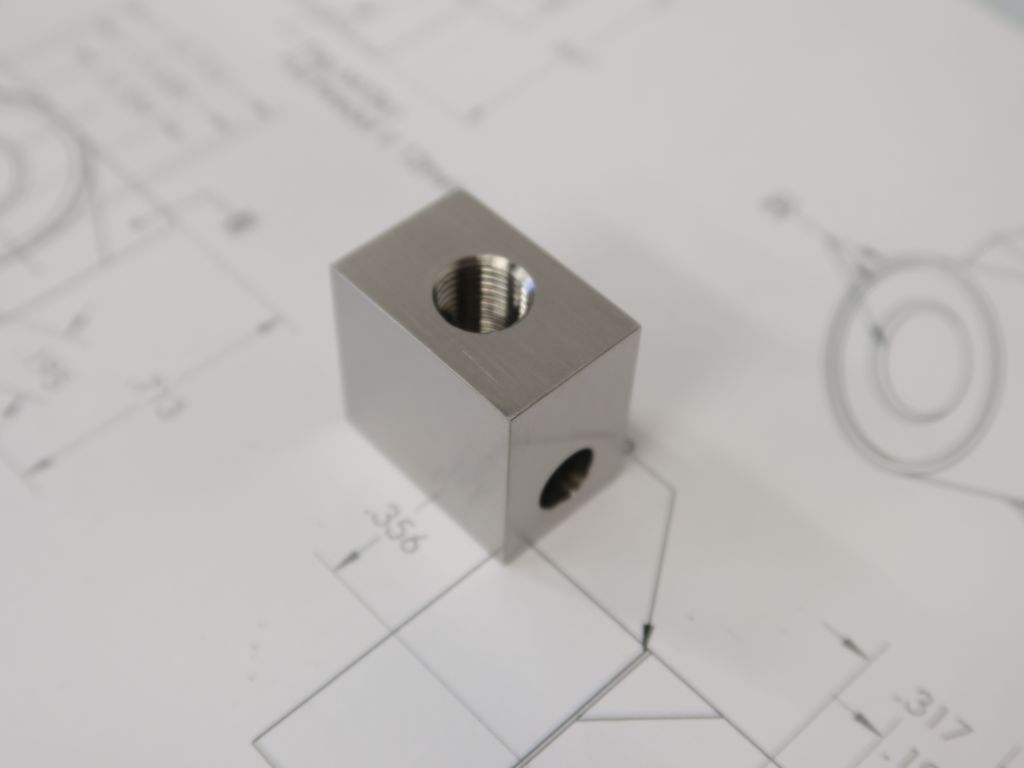
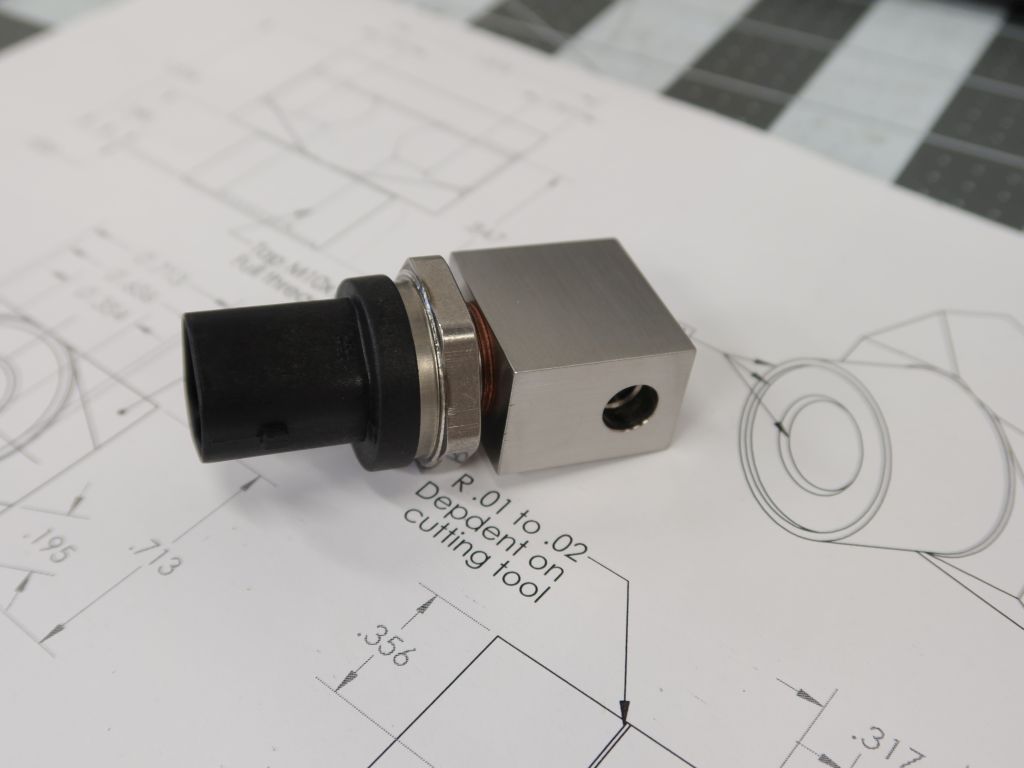
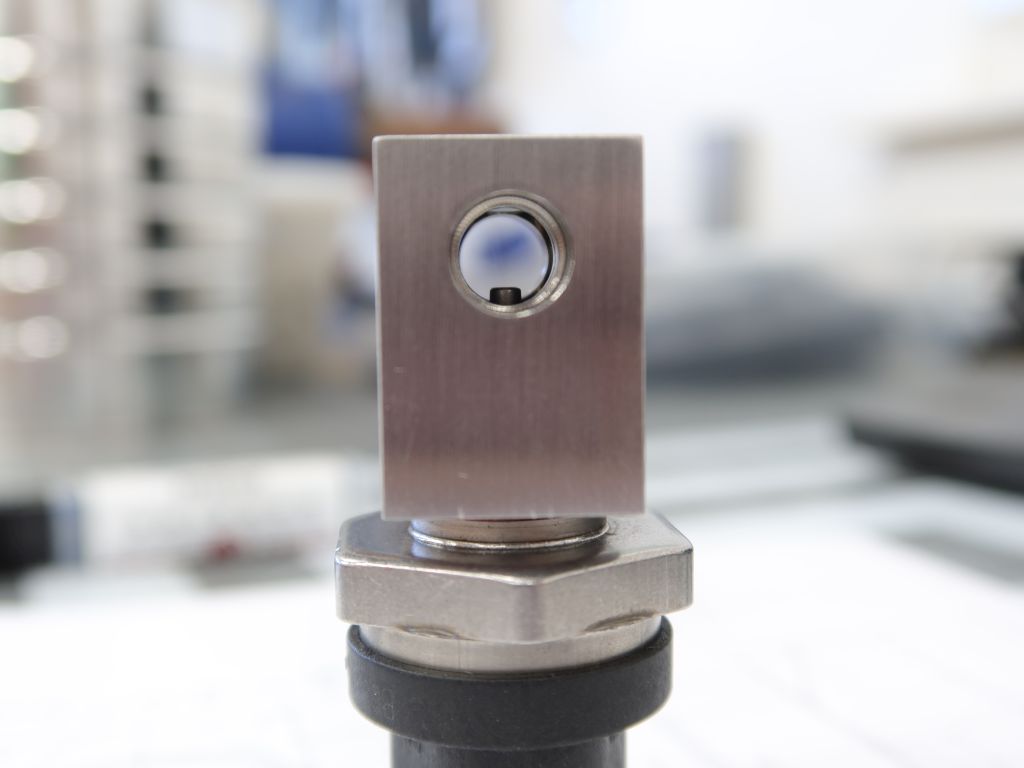
Comment